General
This is a new project for our Australian client.
It is a steering box mount part used for an auto. Our client will make the final machining before use.
Picture
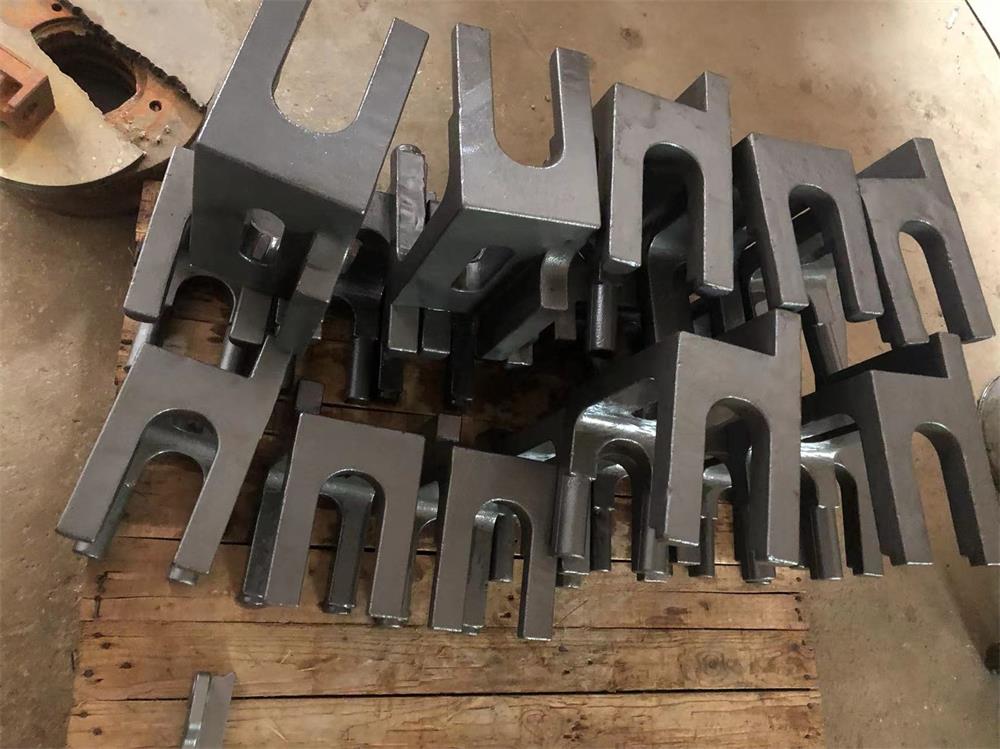
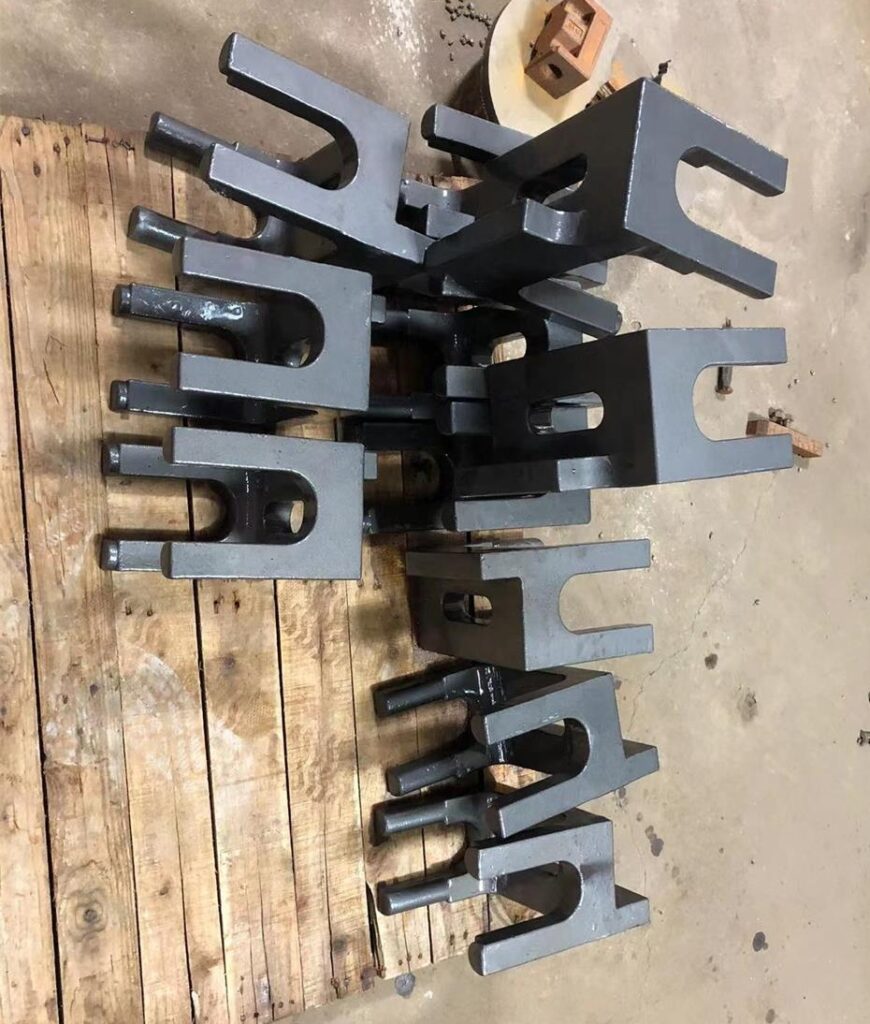
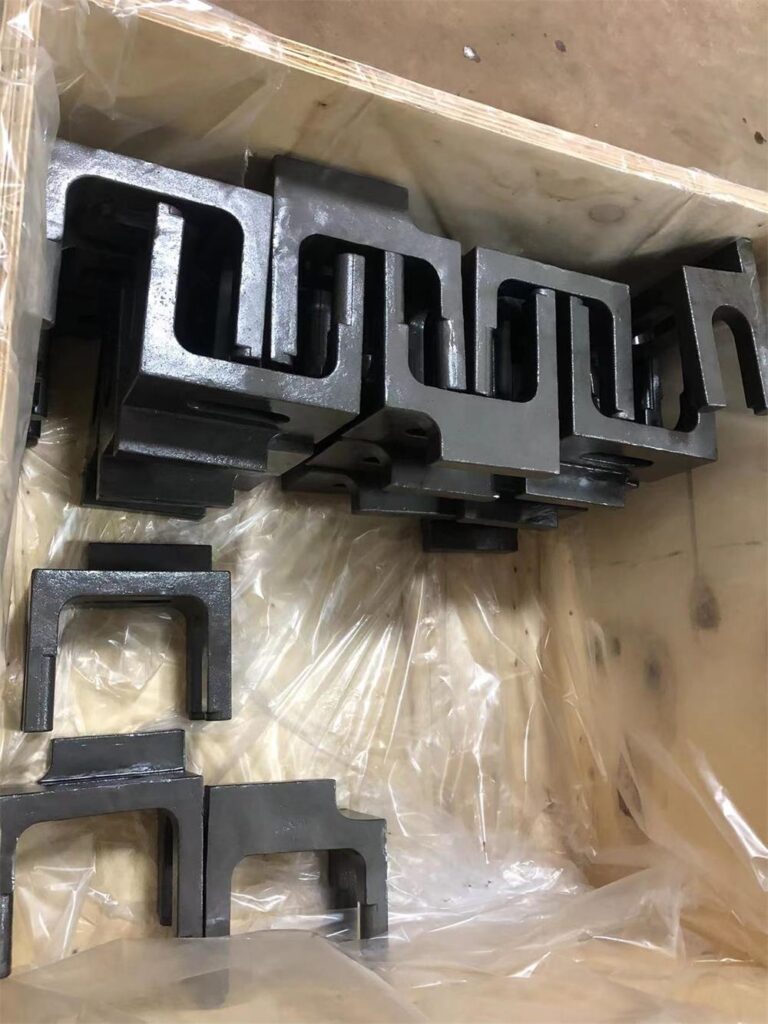
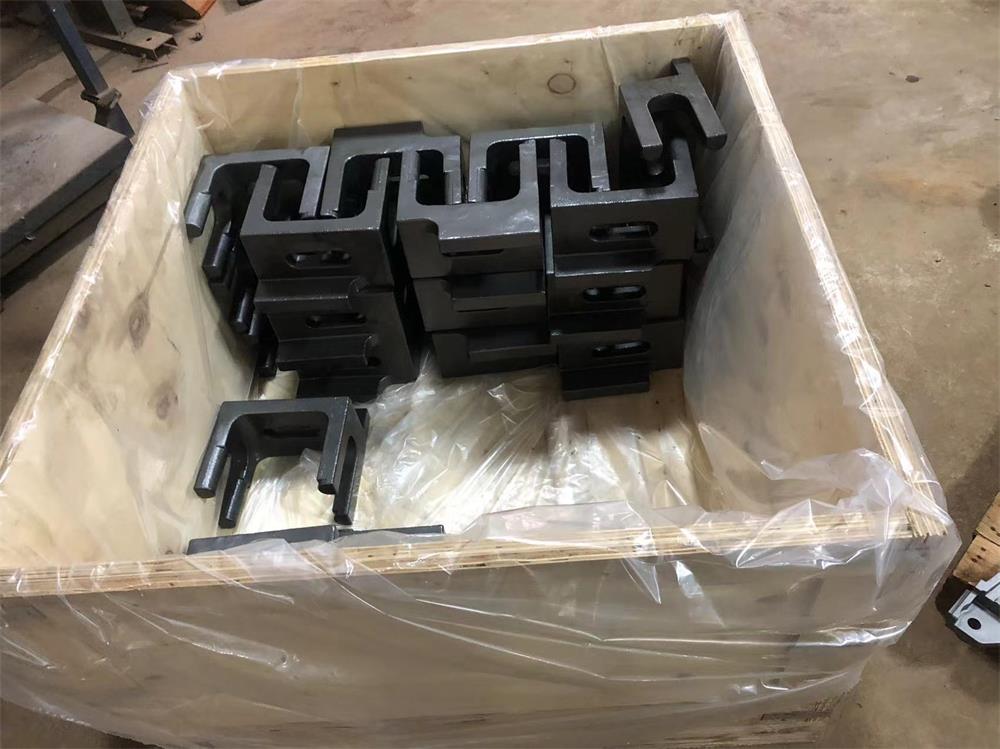
Material
Alloy steel 1025
Quantity
Only 40pcs for the first batch.
Manufacturing Process
Waterglass lost wax casting process. We need to make the new mould first and then manufacture the precision parts.
Surface
Surface finishing: 3.2-6.3RA.
We have two kinds of precision investment casting processes. One is water glass foundry, another is silica sol casting. Silica sol casting is more precise, the finishing is 3.2-6.3RA.
You could refer to the pictures in this link, most of the products here are made by silica sol precision investment foundry.
https://www.ytcasting.com/metal-casting-process/precision-investment-casting/
What is water glass precision investment casting?
Waterglass precision investment casting, also known as the water glass investment casting process, is a specific method used to create intricate and precise metal parts or components. It is a type of investment casting, also called lost wax casting, which has been utilized for centuries to produce complex metal shapes with high accuracy and surface finish.
Here’s an overview of the water glass precision investment casting process:
Pattern creation (mould fabrication)
The process begins with the creation of a wax pattern that replicates the desired shape of the final metal part. The pattern can be produced using various methods, such as injection molding or manual carving.
Assembly
Multiple wax patterns are attached to a central wax gating system to form a cluster of patterns. This cluster is known as a “tree” or “sprue.”
Shell building
The tree of wax patterns is then coated with a ceramic shell. The ceramic shell is typically built up in several layers. The first layer is usually fine ceramic particles mixed with water glass (sodium silicate), which acts as a binder. After the first layer dries, additional layers of ceramic slurry mixed with progressively coarser ceramic particles are applied. This creates a strong and refractory shell around the wax patterns.
Dewaxing
The entire assembly is then heated in an autoclave or furnace to melt and remove the wax from the ceramic shell. This process is called dewaxing, and it leaves behind a cavity in the shell, which will be filled with molten metal.
Preheating
Once the wax is removed, the ceramic shell is preheated to a specific temperature to prepare it for the pouring of molten metal.
Casting
Molten metal is poured into the preheated ceramic shell through the gating system. The metal fills the cavity left by the wax pattern, taking its shape.
Cooling and solidification
The filled ceramic shell, now containing the molten metal, is allowed to cool and solidify.
Shell removal
Once the metal has solidified, the ceramic shell is broken or removed to reveal the metal parts inside.
Finishing
The cast metal parts may require some post-processing, such as cutting off the gating system, removing any excess material, and surface finishing.
Overall, water glass precision investment casting is suitable for producing parts with complex geometries and fine details, making it a preferred method for applications in aerospace, automotive, medical, and various industrial sectors. The process allows for tight tolerances and excellent surface quality, resulting in high-precision components. However, it may be more time-consuming and expensive compared to other casting methods, which should be considered when selecting the appropriate manufacturing process for a specific project.