The manufacturing process of a copper bushing involves several steps:
Material Selection:
High-quality copper alloys, such as bronze or brass, are chosen for their durability and heat resistance.
Mold Preparation
A mold is created with a cavity in the desired shape of the final product. The mold is usually made of a refractory material that can withstand high temperatures.
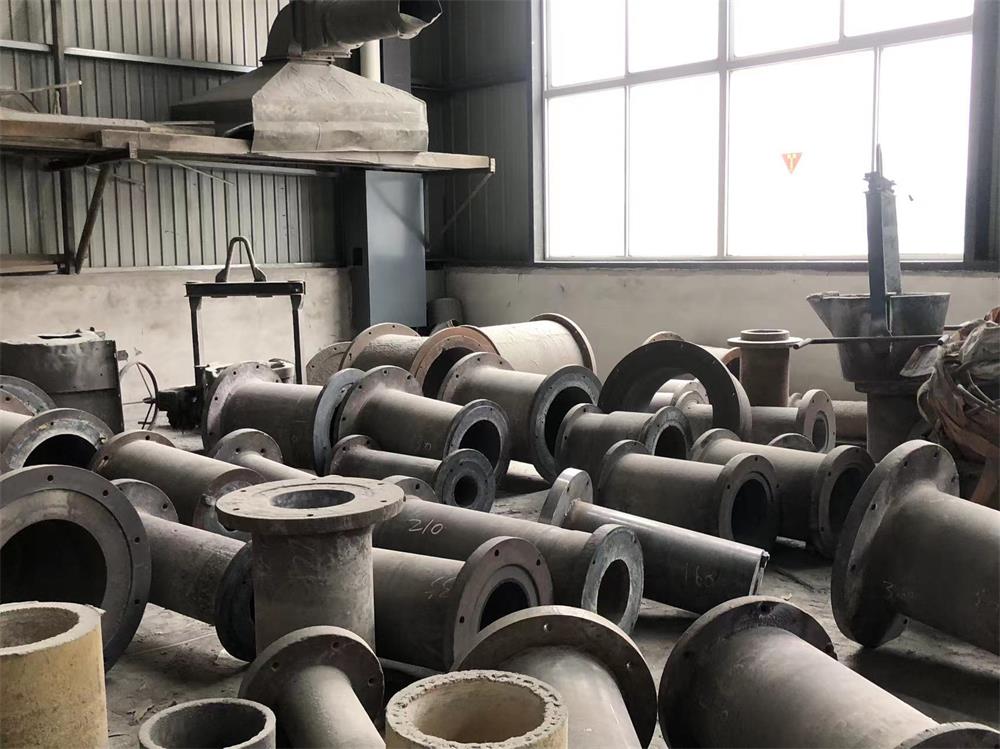
Melting and Casting:
The chosen copper alloy is melted in a furnace and then poured into a mold in the desired shape of the bushing. We use the centrifugal casting.
Centrifugal casting is a manufacturing process used to produce cylindrical or symmetrical hollow parts, such as pipes, tubes, or bushings, with a high level of integrity and precision. It involves the use of centrifugal force to distribute molten metal or other materials into a mold.
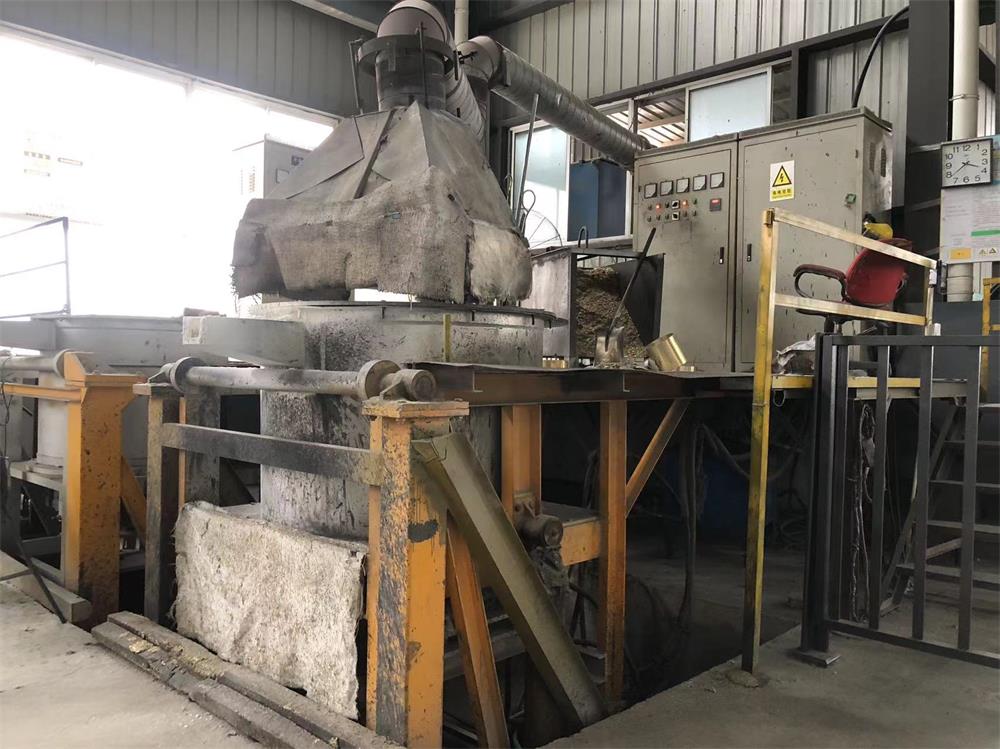
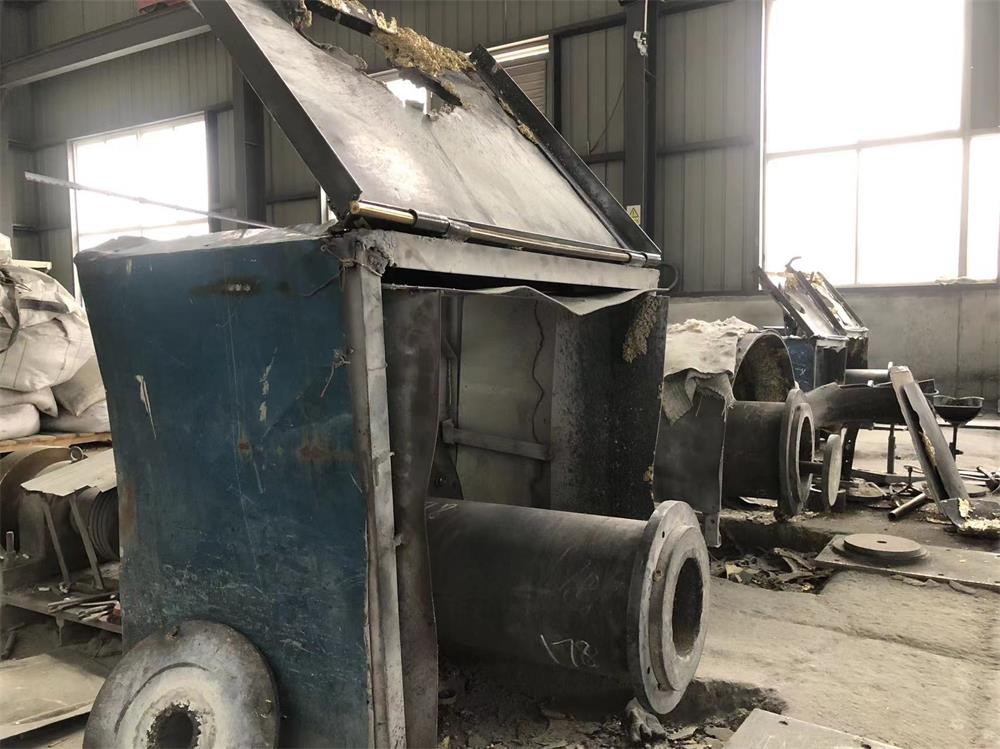
Centrifugal casting offers several advantages, including improved casting density, reduced porosity, better mechanical properties, and enhanced resistance to defects compared to other casting methods. It is commonly used in industries such as automotive, aerospace, marine, and manufacturing, where high-quality, high-strength, and dimensionally accurate parts are required.
Cooling and Solidification
The molten copper alloy is allowed to cool and solidify, forming a solid metal casting.
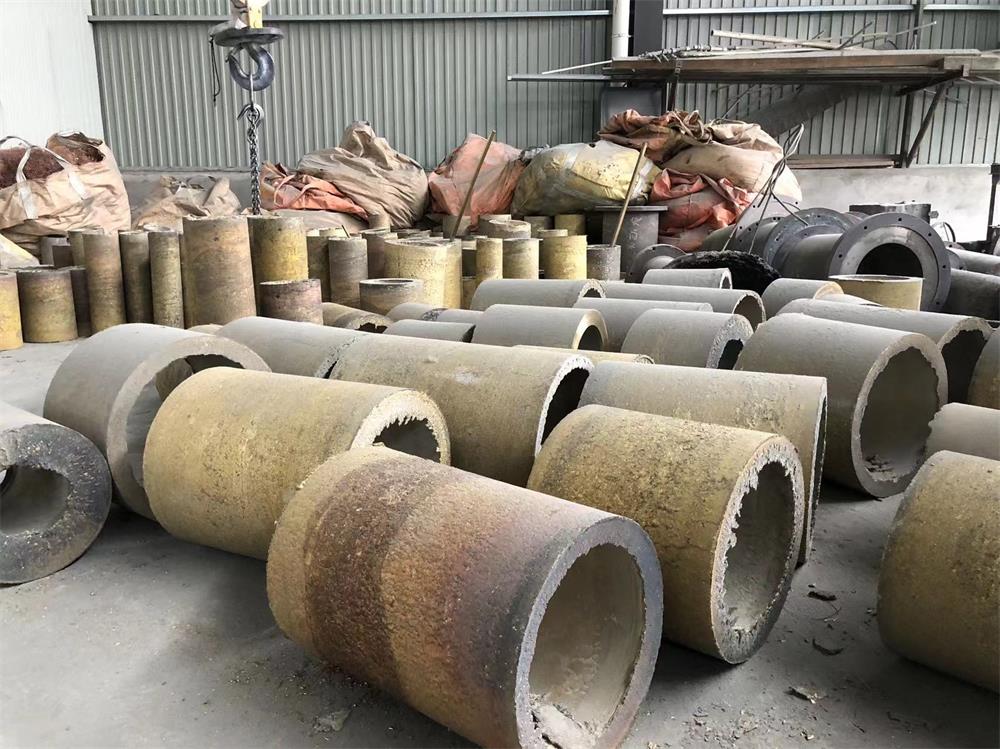
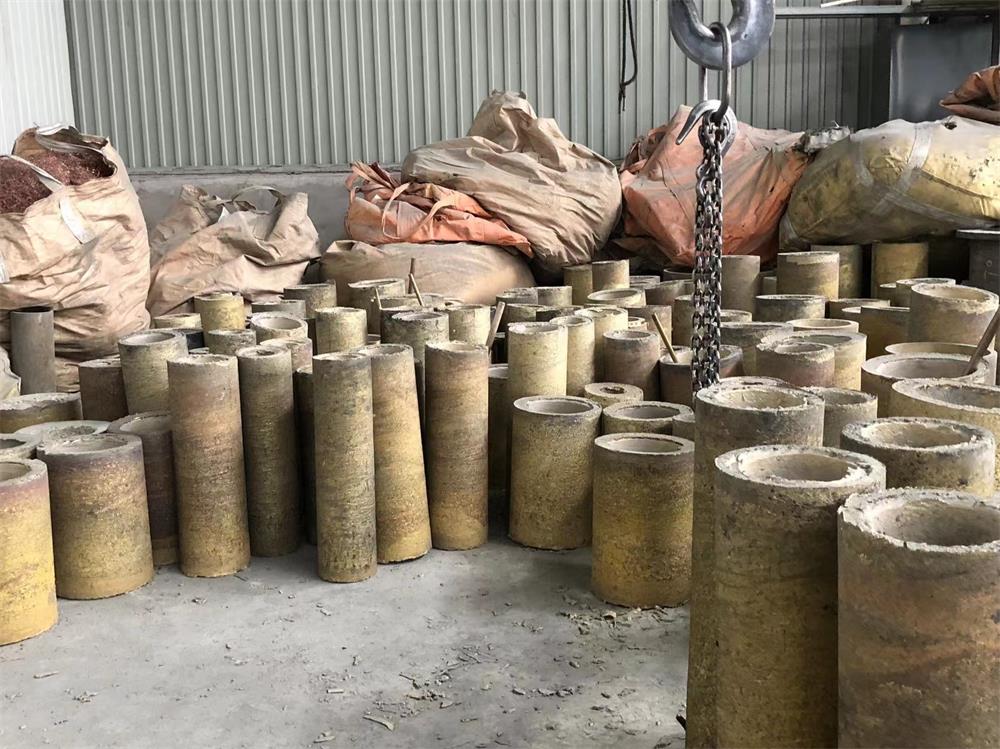
Rough Machining
The rough casting is then machined using various cutting tools to remove excess material and achieve the desired dimensions and shape.
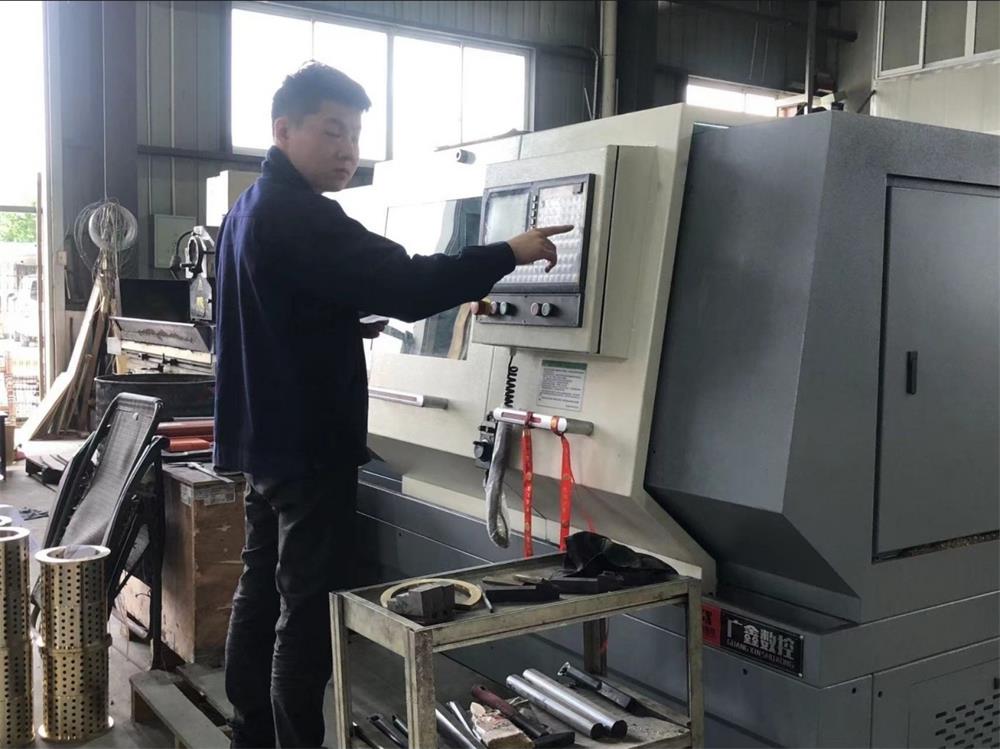
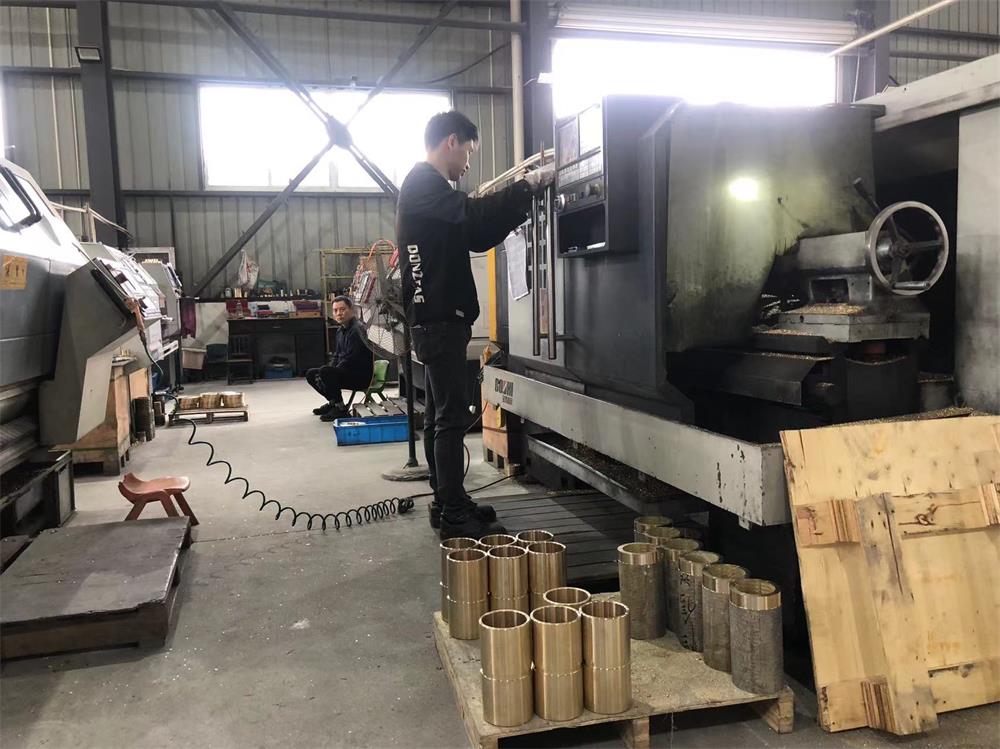
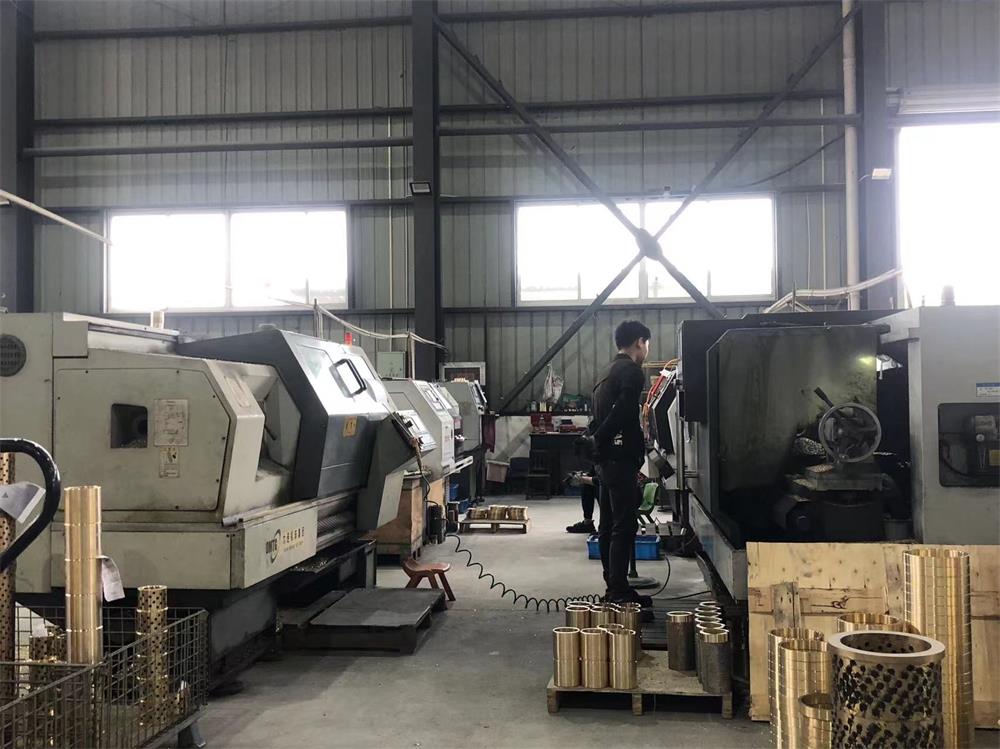
Heat Treatment
The machined copper bushing may undergo heat treatment processes like annealing or tempering to improve its mechanical properties, such as hardness and strength.
Precision Machining
The heat-treated bushing is subjected to precision machining, where it is further shaped and refined to meet tight tolerances and smooth surfaces.
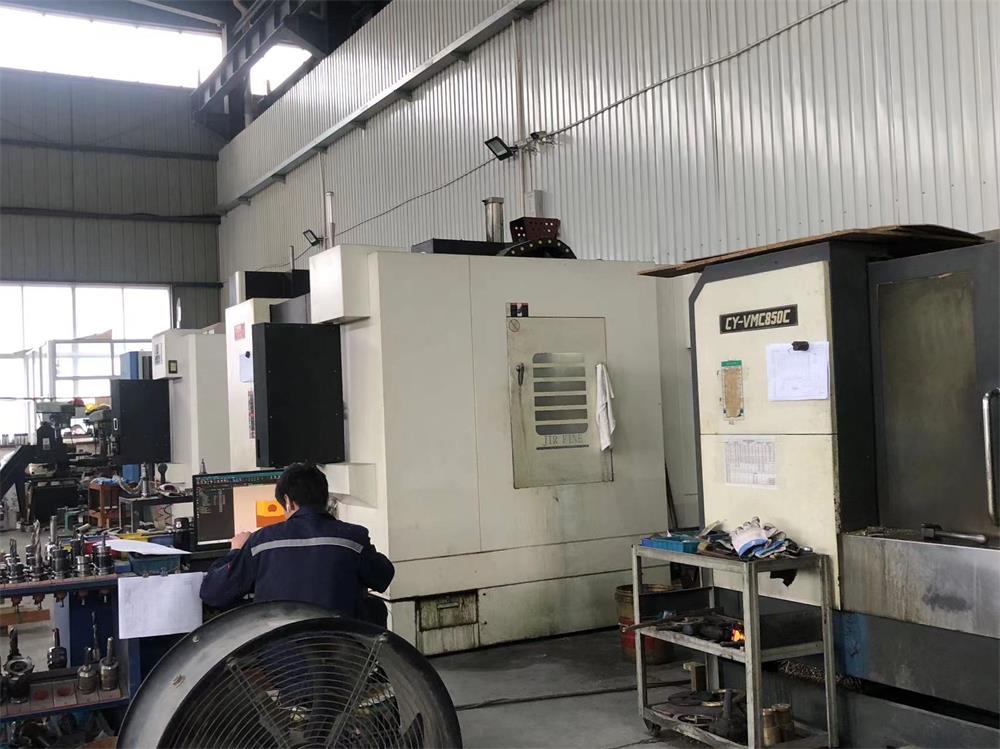
Surface Finishing
The copper bushing may undergo surface treatments like polishing, grinding, or coating to enhance its appearance, corrosion resistance, and reduce friction.
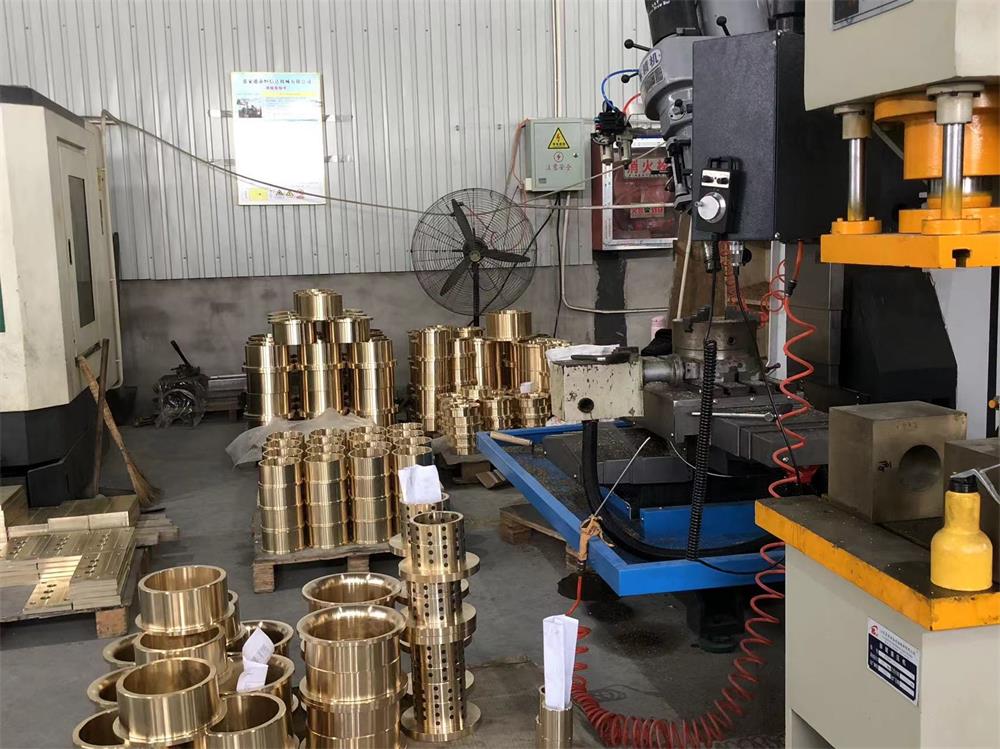
Quality Inspection
Throughout the manufacturing process, rigorous quality checks are conducted to ensure the bushing meets specified standards for dimensions, surface finish, and mechanical properties.
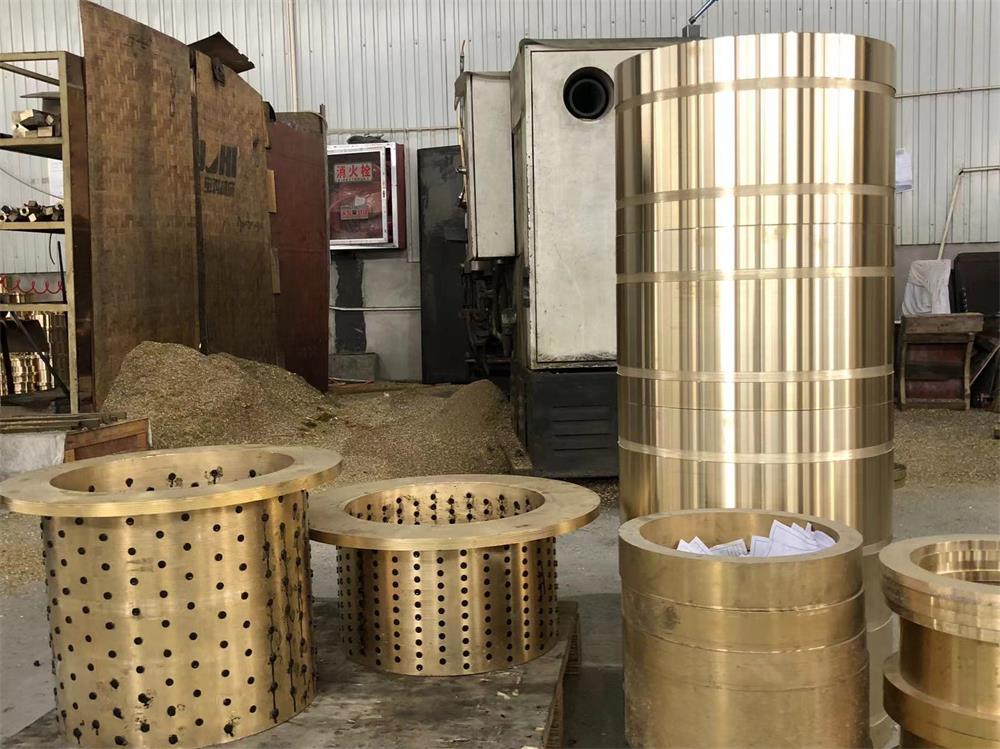
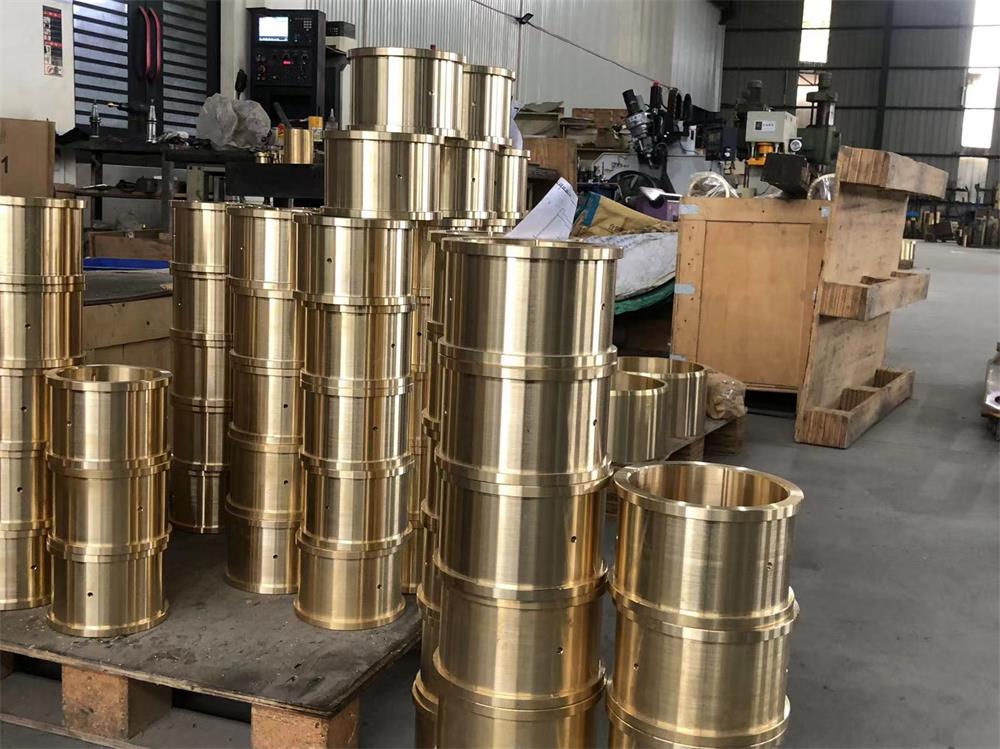
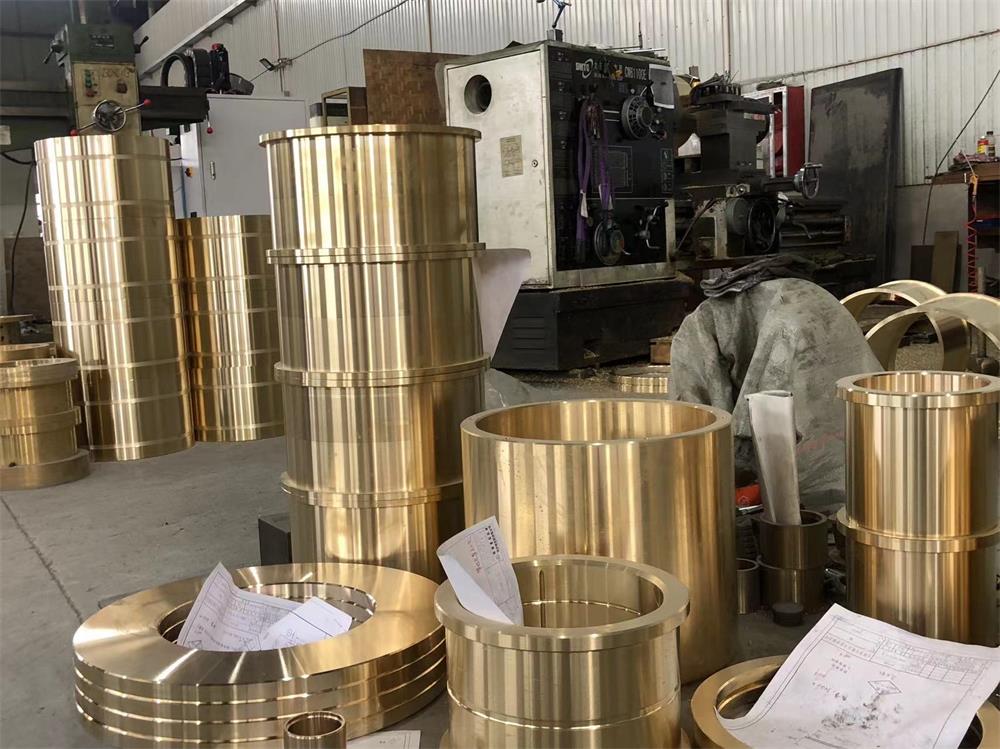
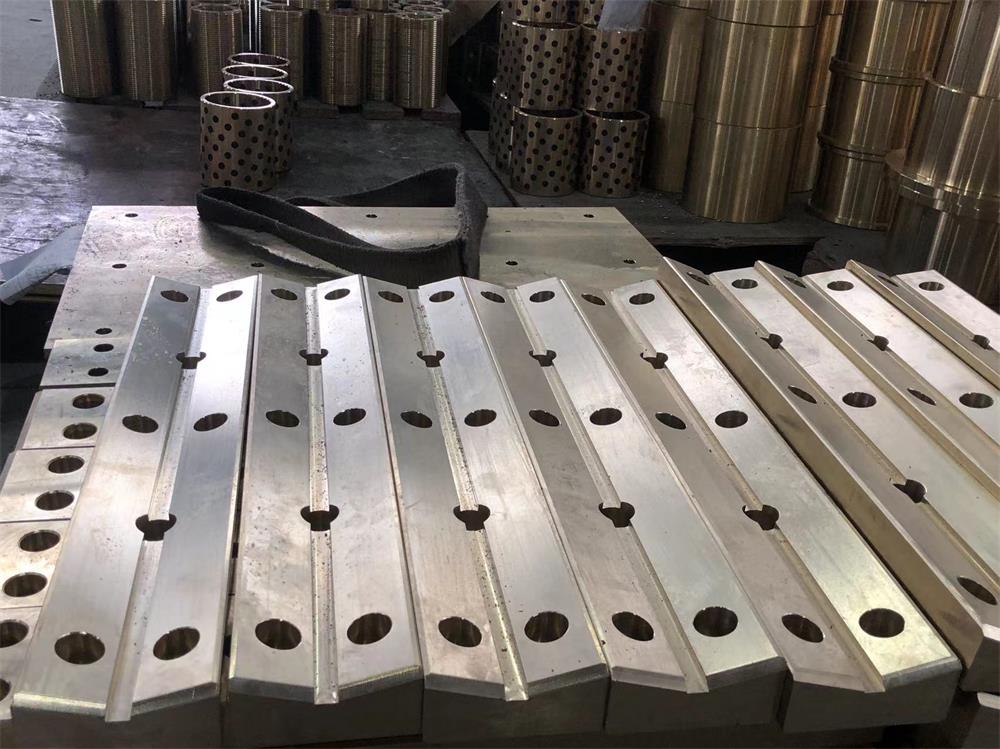
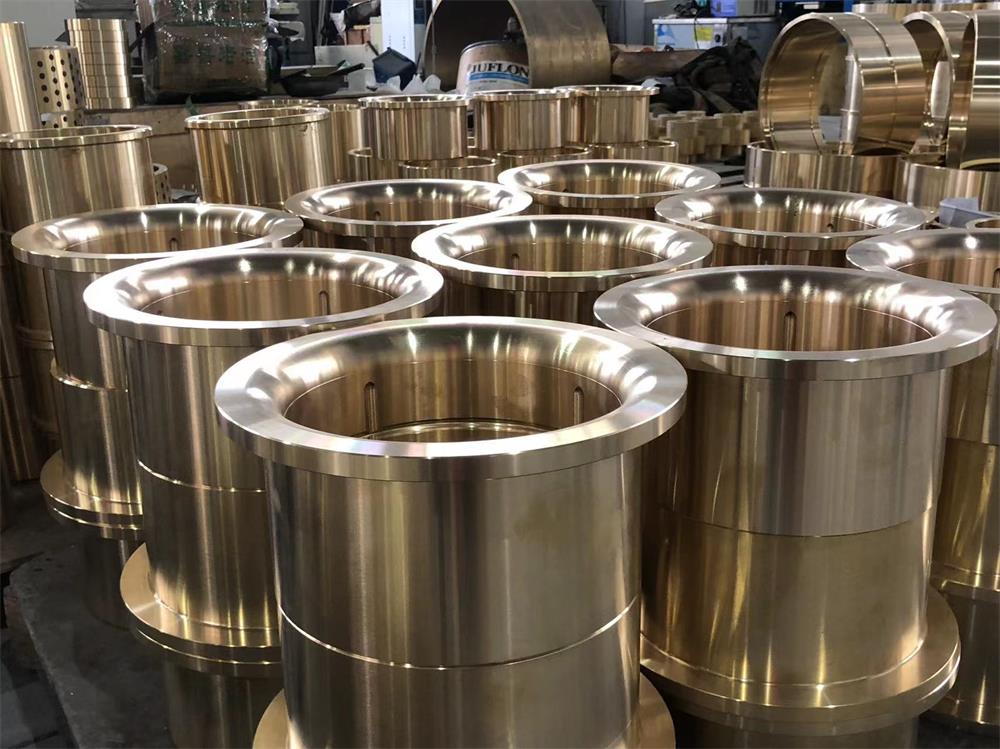
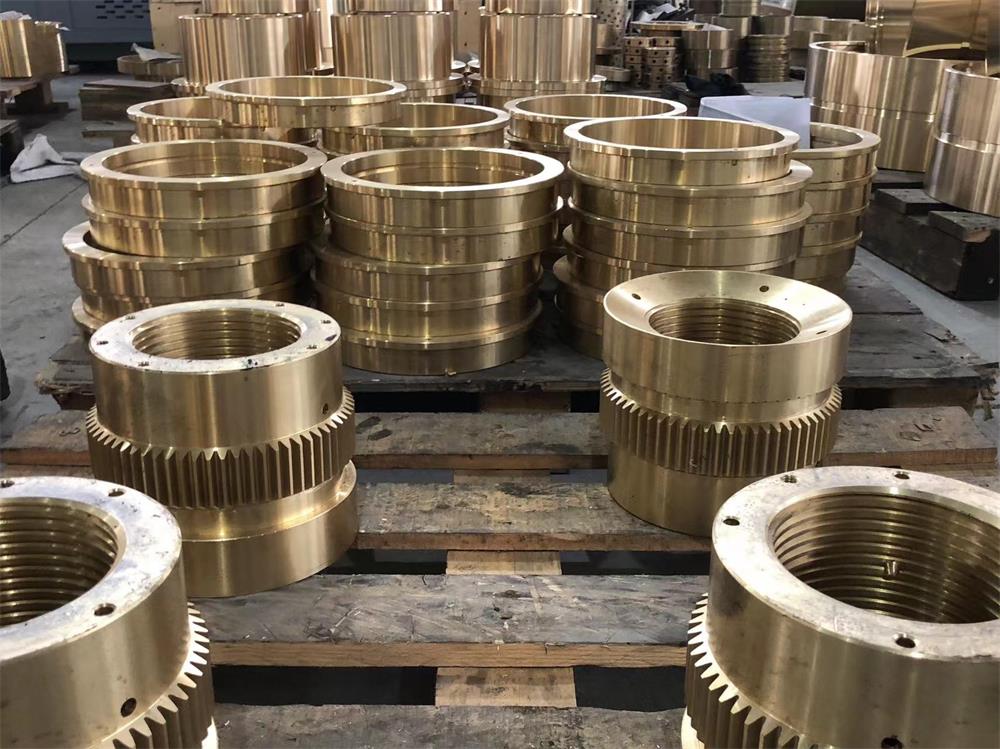
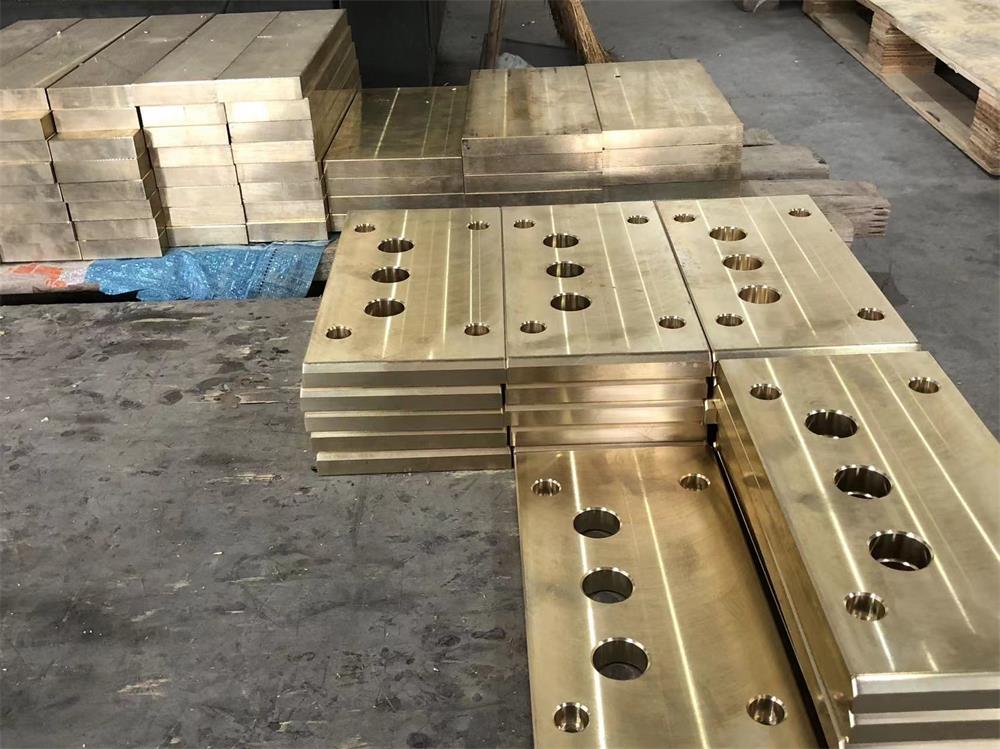
Assembly or Packaging
:Once the copper bushing passes inspection, it can be assembled into the intended product or packaged for shipment to customers.
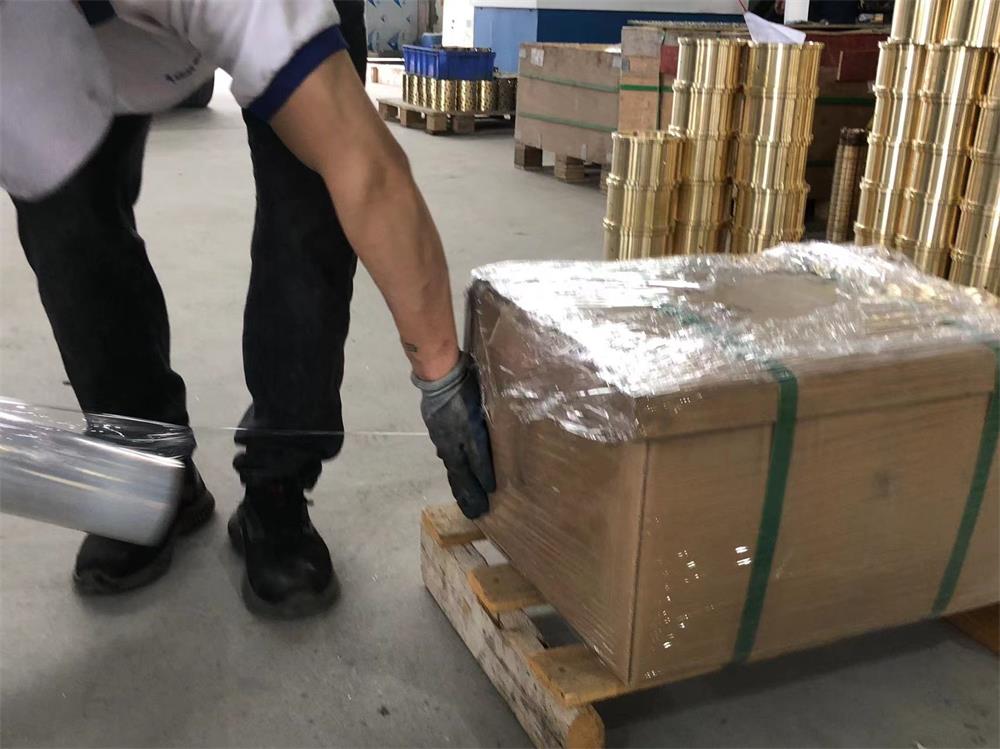
Copper Recycle Material
The machined copper material will be melted for re-use.
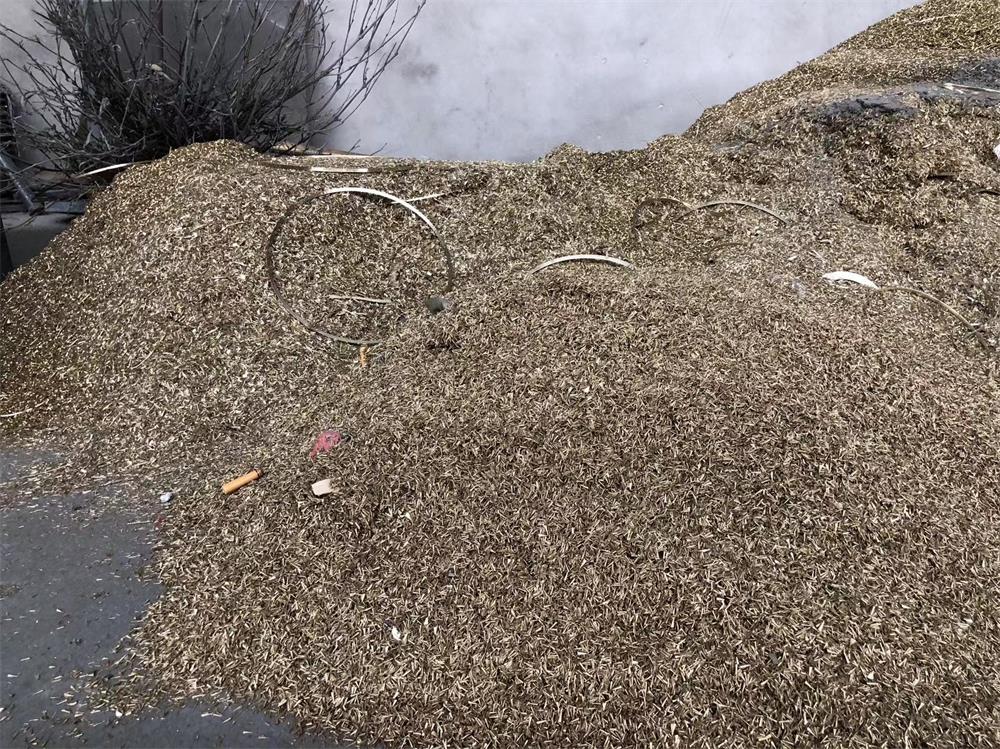
Application
The finished copper bushing is then ready to be used in various industrial applications, such as automotive engines, machinery, electrical equipment, or plumbing systems.
Please note that the specific manufacturing process may vary depending on the desired type and size of the copper bushing, as well as the manufacturer’s techniques and equipment.
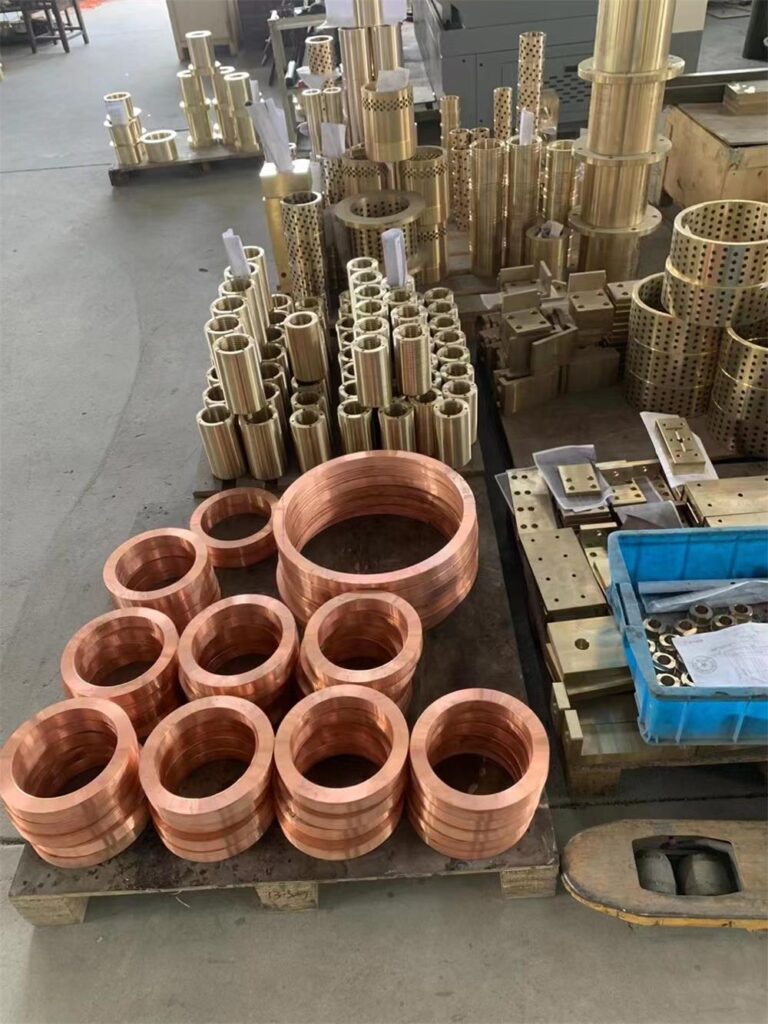
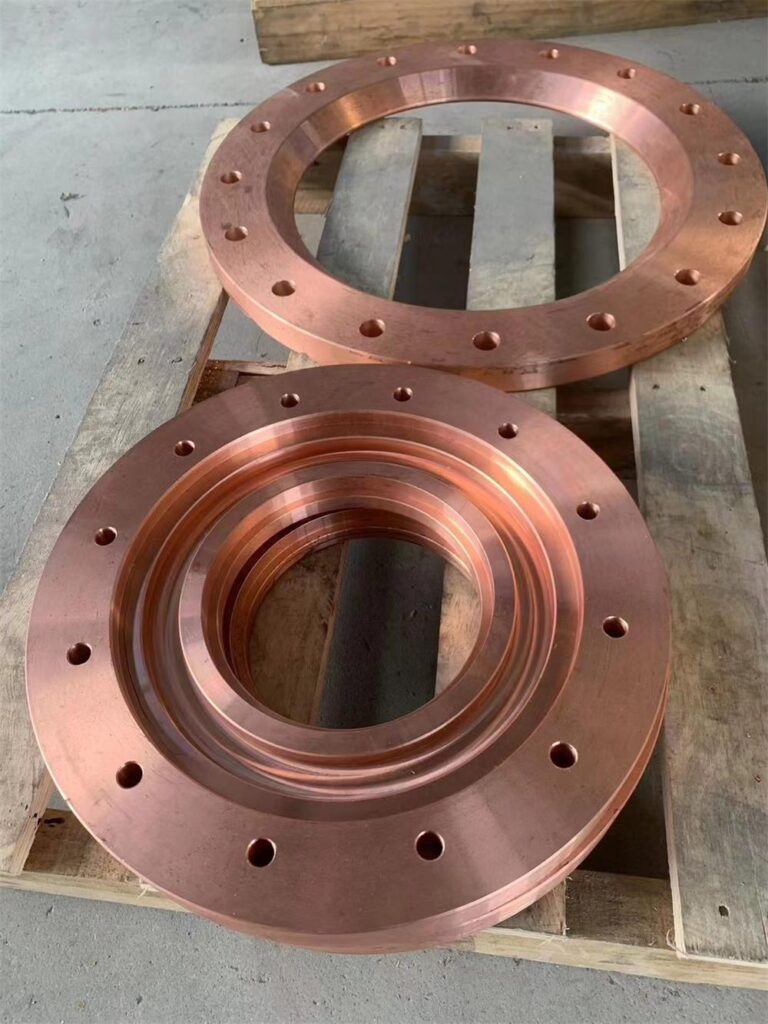
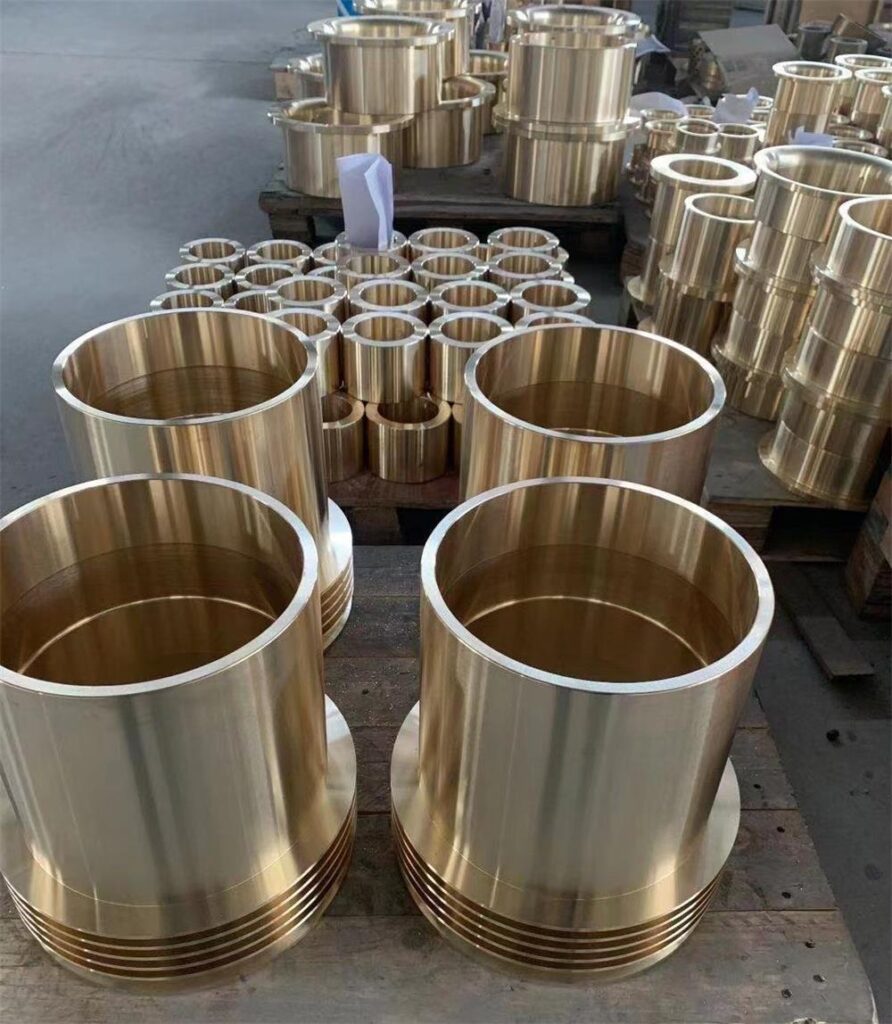
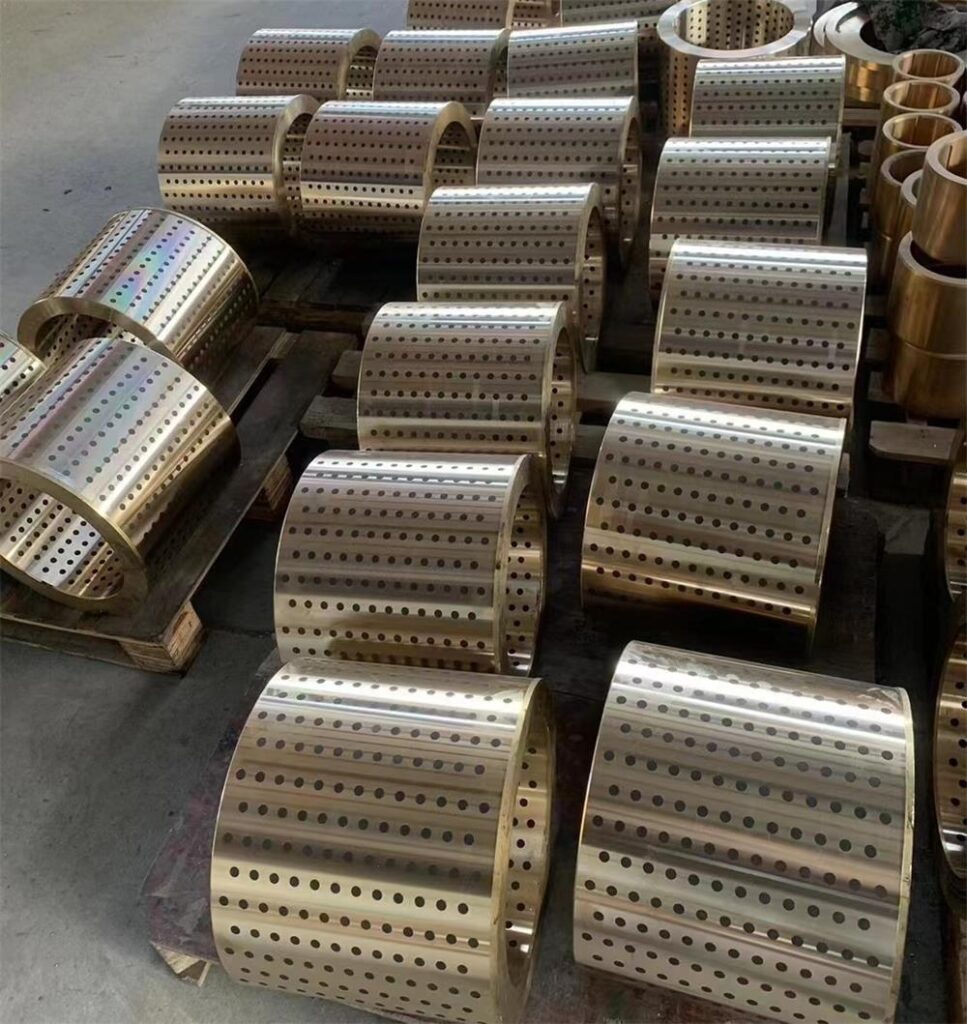
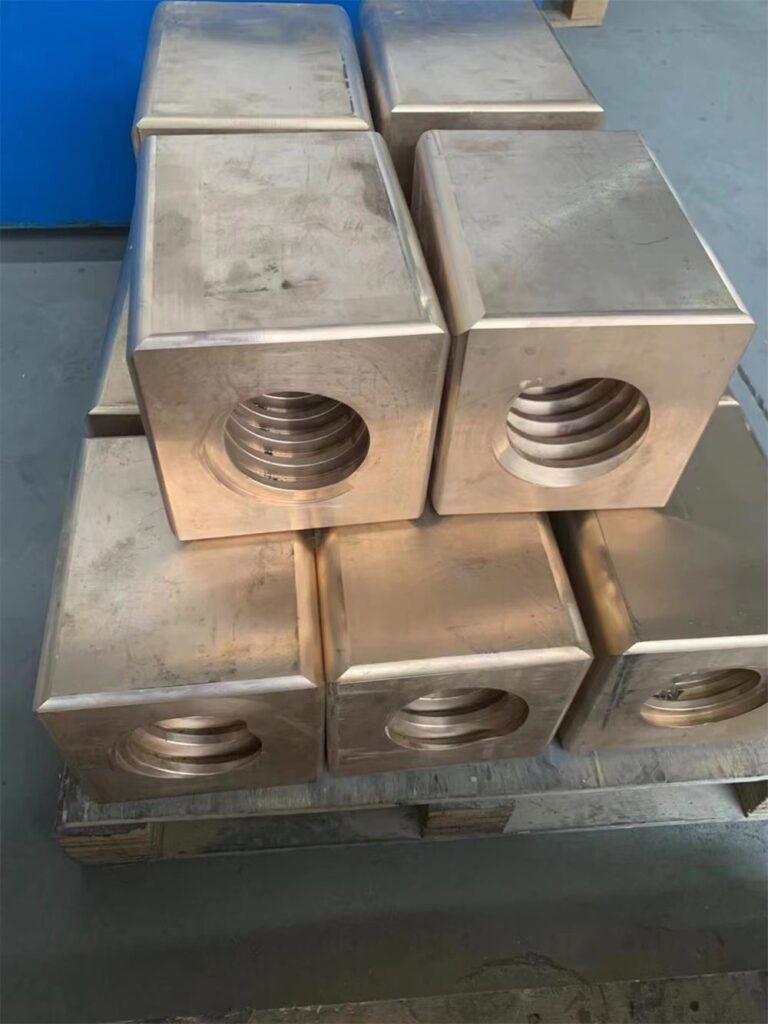
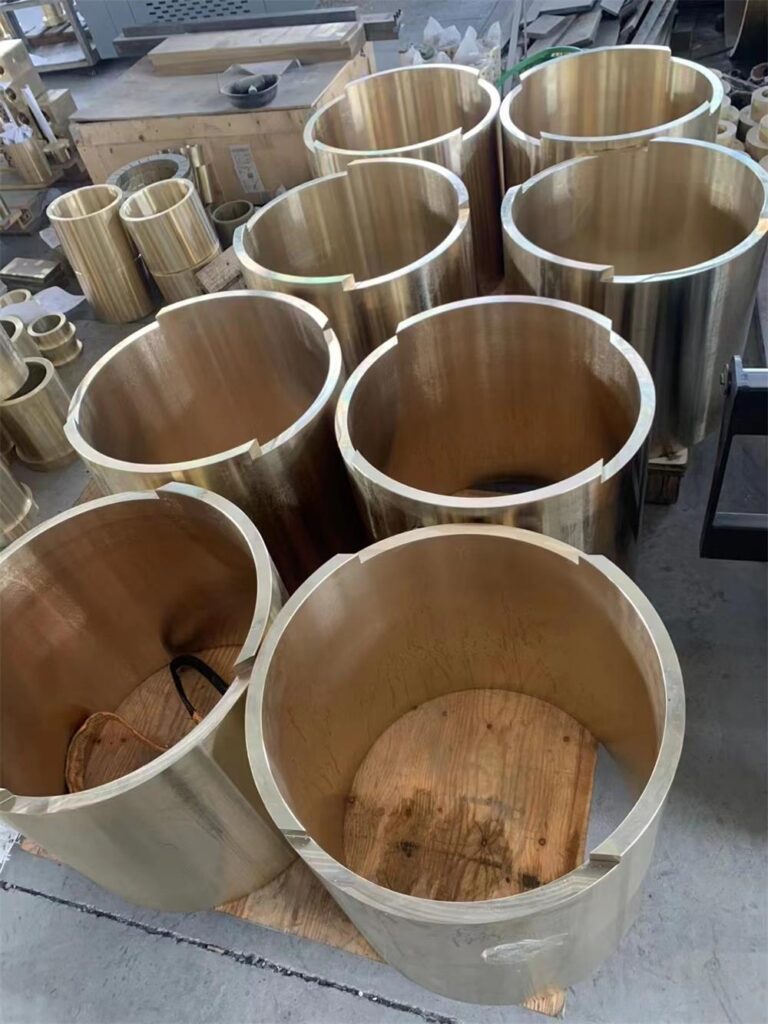
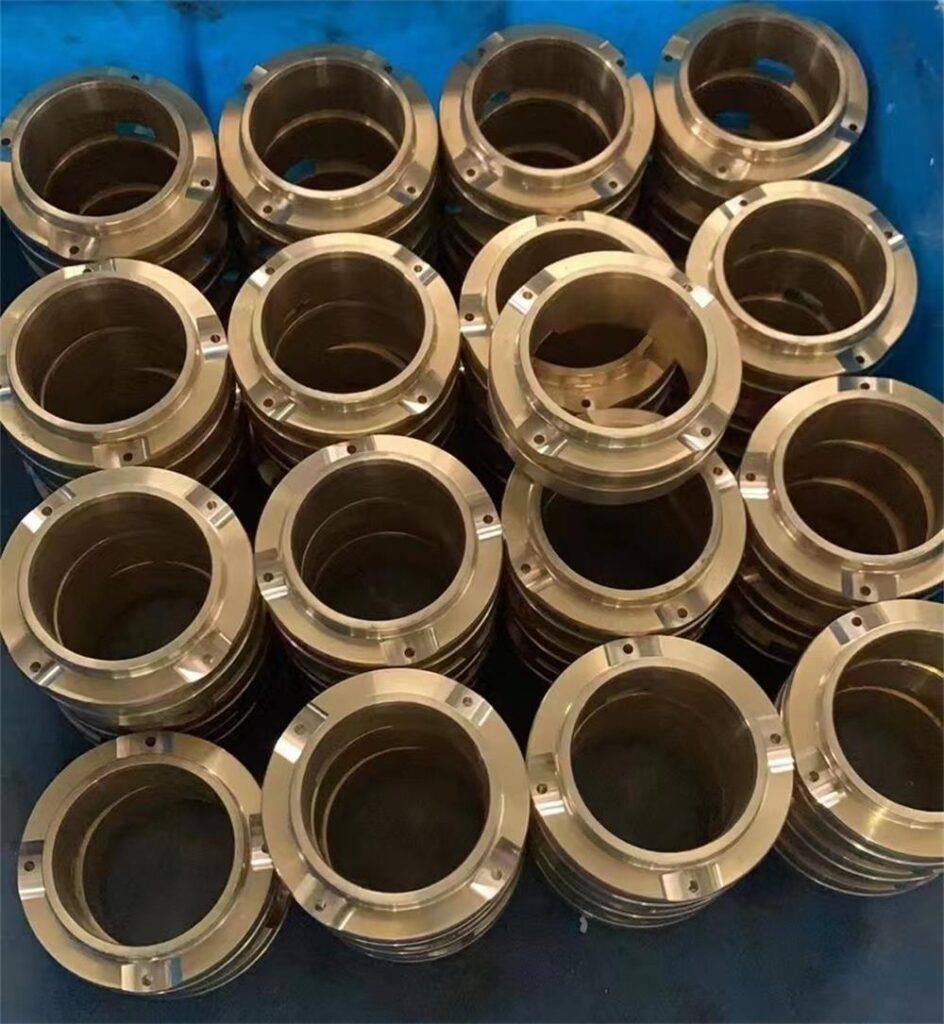
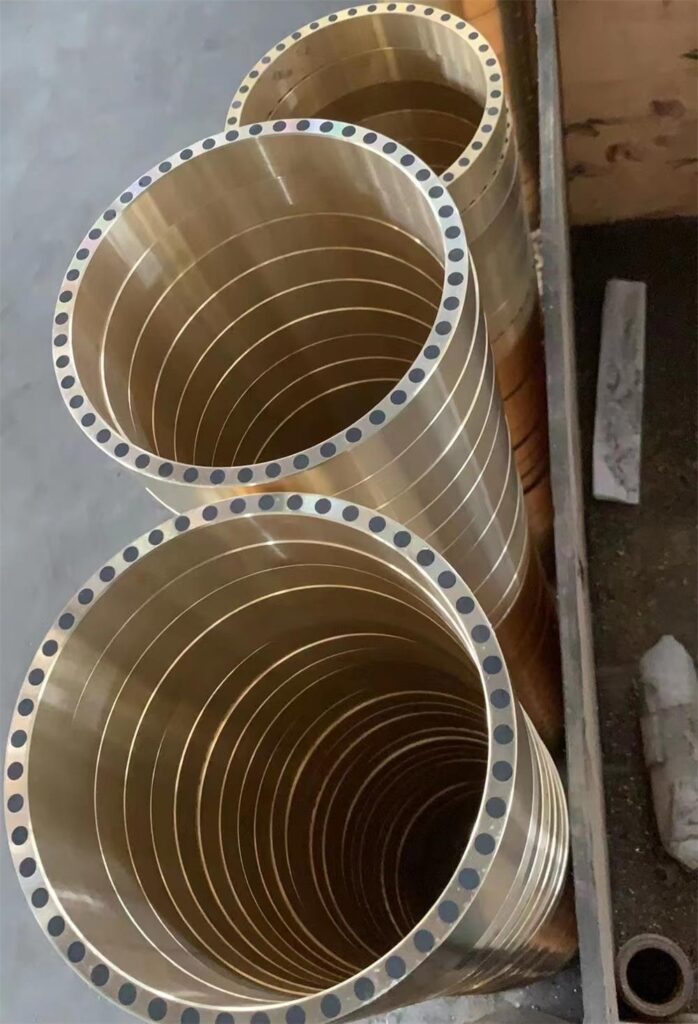
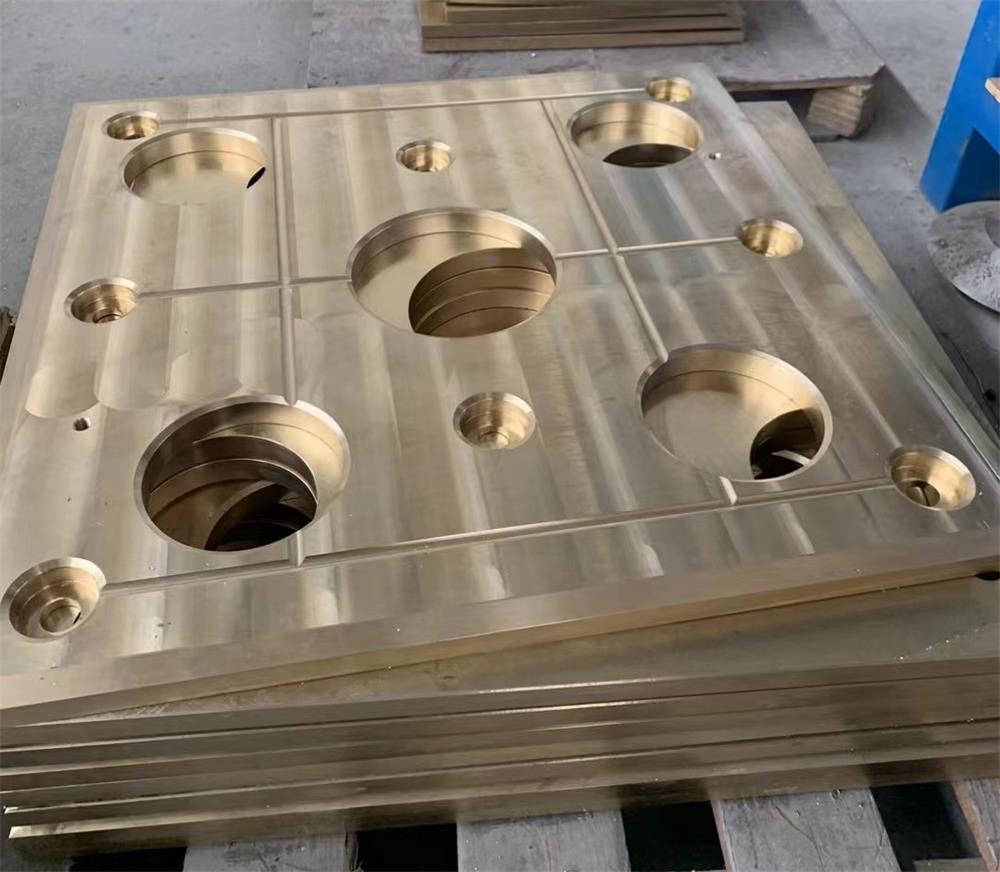
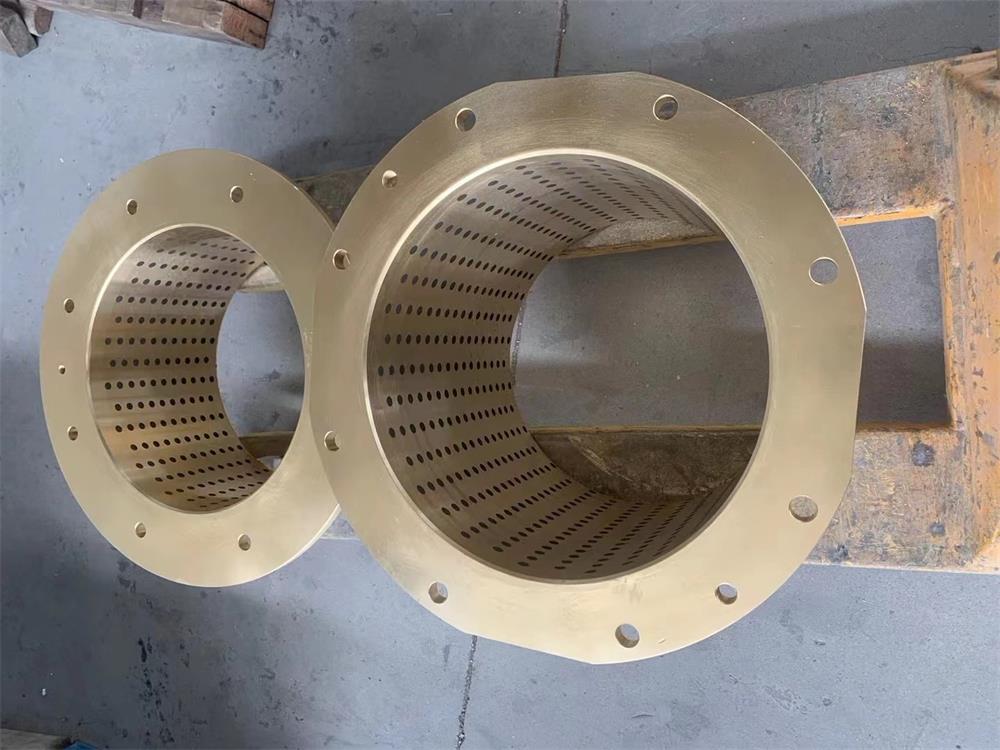
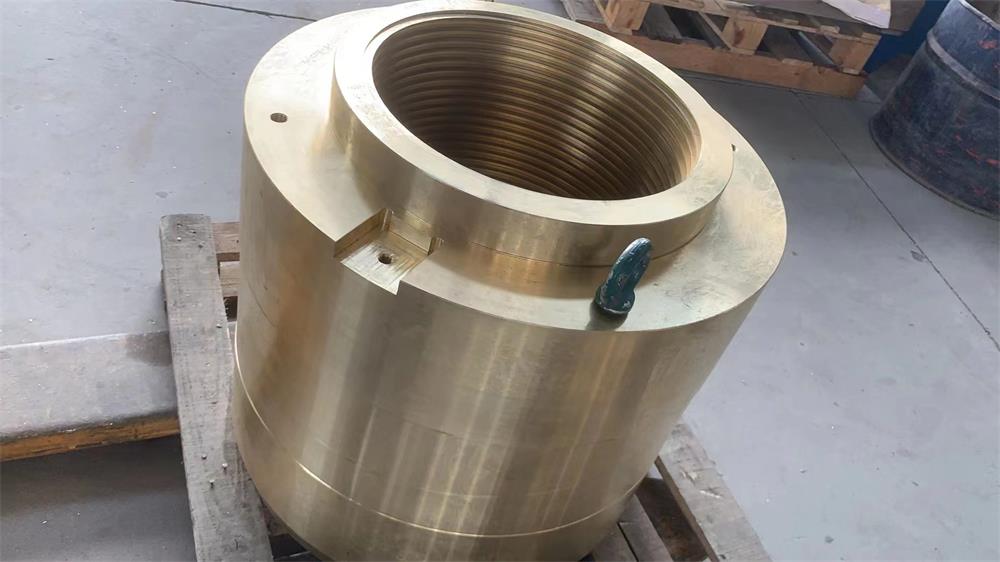